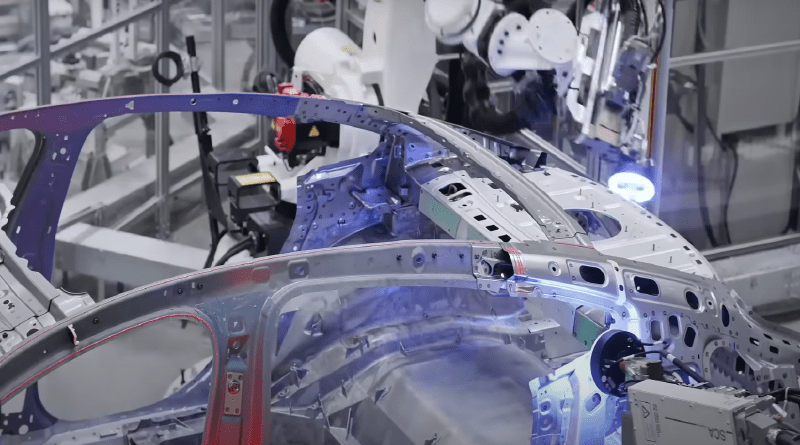
Automotive EV Smart Factory Focussed on Automated Quality Control
Chinese smartphone maker Xiaomi has become China’s eighth-largest electric vehicle manufacturer after launching its SU7 sedan model, in April. Xiaomi’s entry into the crowded China EV market is set to further disrupt the world’s largest auto market. Xiaomi is a household name in China renowned for its smartphone and home appliance products.

Founder and CEO Lei Jun claims the Xiaomi Smart Super Factory can build 40 SU7 vehicles per hour. More than 700 robots operate throughout the factory. In the body shop, 20 human workers are assisted by 381 robots, with eight robots per workstation.
Key Features of Xiaomi’s Smart EV Factory include:
Unmatched Automation: A team of 269 robots seamlessly collaborate to assemble the Xiaomi SU7 with pinpoint precision and efficiency. This level of automation minimizes human error and ensures consistent quality throughout the production process.
Unwavering Quality Control: Xiaomi leverages cutting-edge technology to implement rigorous quality checks at every production stage. This dedication to excellence ensures every SU7 that rolls off the line meets the highest quality standards.

Advanced Quality Control Technology
Nikon’s APDIS Laser Radar is being used as an integral part of the fully automated production line. Within the fully automated cell, two APDIS Laser Radars on 7 axis robots measure the body frame for 100% online inspection with the Laser Radars, while the BIW is moved automatically through the production line.

A second inspection cell with robot mounted APDIS Laser Radar with turntables measure front and rear structures for the electric vehicle’s BIW structure before assembly in a side spur of the main production line.

The X-Eye, Xiaomi internally developed, robot mounted X-ray inspection system checks hypercastings for defects with an accuracy rate exceeding 99%.
Machine vision systems are a feature of the automated vehicle production facility created by Xiaomi with many of the installed systems providing data dynamically allowing for adaptive process control and assembly processes.