风电叶片是风力发电系统的重要组成部分,其生产成本占整机总成本的五分之一左右,在系统中扮演着将风能转换为电能的关键角色:风带动叶片转动,将风能转换为机械能;叶片旋转的动力通过齿轮箱等传动系统,提高转速,并将机械能传递给发电机;发电机利用电磁感应原理将机械能转化为电能。 图 1 风能发电流程
目前现役和在产的风电叶片大多由玻璃纤维复合材料制成,具有轻质、高强度、高刚度等优点。受限于生产工艺,难免会产生一些缺陷,这些缺陷随着运行时间延长而不断累计,从而导致叶片失稳损坏。因此,在叶片制造成型后或安装前进行检测,确认其是否存在缺陷,是保证整套风电机组安全运行的重要保障。 图 2 叶片工件和现场
1、 叶片结构
风电叶片一般为中空薄壁结构,主要由外壳和主梁两大部分构成,辅以外壳蒙皮和其他泡沫、木板填充材料,形成完整的叶片。外壳和主梁由玻璃纤维复合材料制成,占整个风电叶片总质量的90%以上,是检测工作的重点关注对象。

图 3 叶片结构
2、缺陷类型 叶片制造时首先通过专用模具分别成型外壳和主梁等部件,再将各部件粘连形成完整的叶片,在这两道工序中由于工艺局限性或者人员操作问题,可能会出现各种不同的缺陷。模具成型过程可能出现分层、孔隙、干纤维等缺陷,部件粘连过程可能出现缺胶、外壳与主梁/蒙皮粘连不佳等缺陷。
风电叶片的主要由玻璃纤维复合材料制成,故可以参照复合材料检测相关标准进行检测,目前常用的复合材料风电叶片无损检测技术有以下几种:
目视法检测
通过肉眼或借助放大镜发现缺陷,但仅限于叶片外表面和内腔,局限性大,且受检测人员主观因素影响。
敲击法检测
通过敲击工件发出的声音分辨缺陷,对检测环境和人员的经验要求高,且可能损伤叶片。
X射线检测
检测结果直观,灵敏度高,但较难检测平行于表面的缺陷,且设备庞大、射线对人体有害。
红外热成像检测
设备简单,操作方便,但对材料传热性能要求较高,而且无法对缺陷尺寸进行定量分析。
常规超声检测
受限于探头尺寸和视图显示,只能逐点检测,且只能呈现A扫描波形,检测结果容易受人为操作影响,检出率较低。
现有的常规检测技术组建难以满足需求,促使越来越多的风电叶片生产企业希望能找到更加快速高效、更加准确可靠的检测技术。为满足此需求,SIUI推出了针对风电叶片的超声相控阵检测技术,基于全聚焦超声成像检测仪SyncScan 64PT和高穿透性专用探头,在多个现场取得令人满意的检测效果。
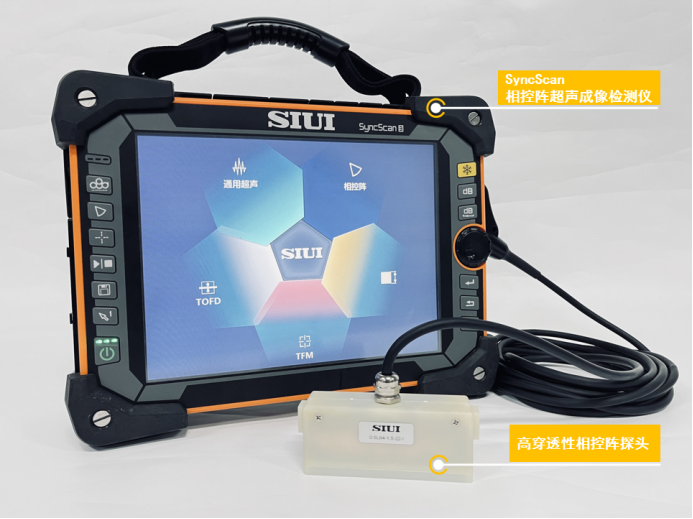
图 5 SyncScan和高穿透性探头
SIUI的相控阵检测方案具有以下优势:
可用于检测各种类型的玻璃纤维复合材料缺陷,如孔隙、分层、粘连不佳等,适用范围广
配套专用的低频高穿透性探头,能够有效完成高衰减性、大厚度的玻璃纤维叶片工件检测
64阵元、1.5间距的探头参数,声束覆盖宽度达到96mm
高能量的灵敏度测量,同时可根据叶片特点灵活改变焦点位置,提高大深度、高衰减缺陷的检出能力
可在不同角度和深度上生成高分辨率图像,清晰显示出叶片复杂结构中的微小缺陷,提高检测准确性
具备3D仿真和无线数据采集等多种功能,使得风电叶片检测的过程更加高效快捷,图像简单明了
我们已经掌握了风电叶片检测的关键方法,随之而来的,是面对风电叶片30到100米的长度,扫查效率如何快速提高这个问题。有经验的相控阵检测人员,很快会想到可以采用扫查装置来实现。然而,手动装置、自动装置、水浸法、反射法、穿透法,各种装置和方法组合不胜枚举,哪种才是最贴合现场使用情况的产品?
带着这个问题,经过大量现场验证,SIUI即将给出答案!
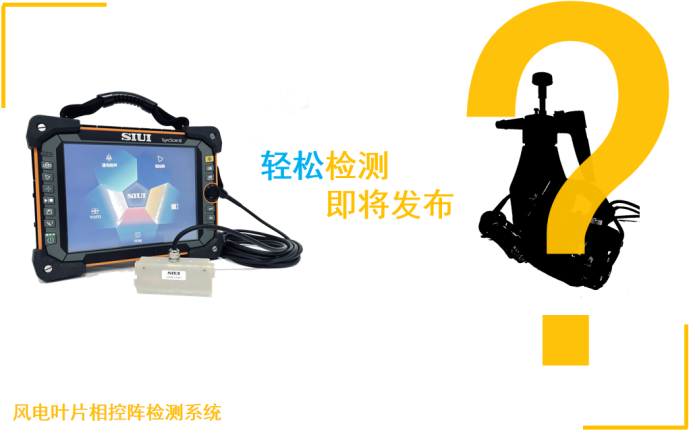