风电作为可再生的清洁能源,随着近年来风机功率大型化的发展,发电成本不断降低,已然成为一种极具竞争力的新能源产品。由于风电设备通常建设在野外或海上环境,长期经受酷暑严寒和侵蚀的影响,服役和维护条件恶劣,需要定期进行检测排查以消除安全隐患。螺栓及塔筒的安全检测至关重要。 风机螺栓,作为连接风机各个部件的关键组件,其重要性不言而喻。一旦螺栓出现问题,可能会导致风机部件松动,甚至引发严重的安全事故。同样,塔筒焊缝也是确保风机稳定运行的重要环节。焊缝的质量直接关系到塔筒的结构强度和稳定性。 为了确保风机螺栓和塔筒焊缝的质量,汕头超声-相控阵检测技术方案应运而生。这种检测技术具有许多优势。首先,它是一种非破坏性检测方法,不会对被检测对象造成任何损伤。其次,超声波检测可以检测到螺栓和焊缝内部的缺陷,如裂纹、气孔、夹渣等,为及时发现和处理潜在问题提供了有力保障。
螺栓连接是风电机组各主要部件的重要连接方式,其工作质量是保证整个风电机组安全和可靠性的关键所在。
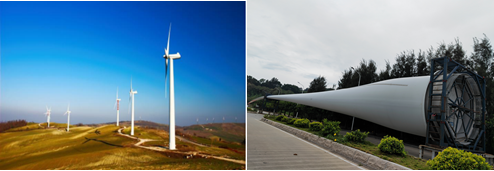
检测对象
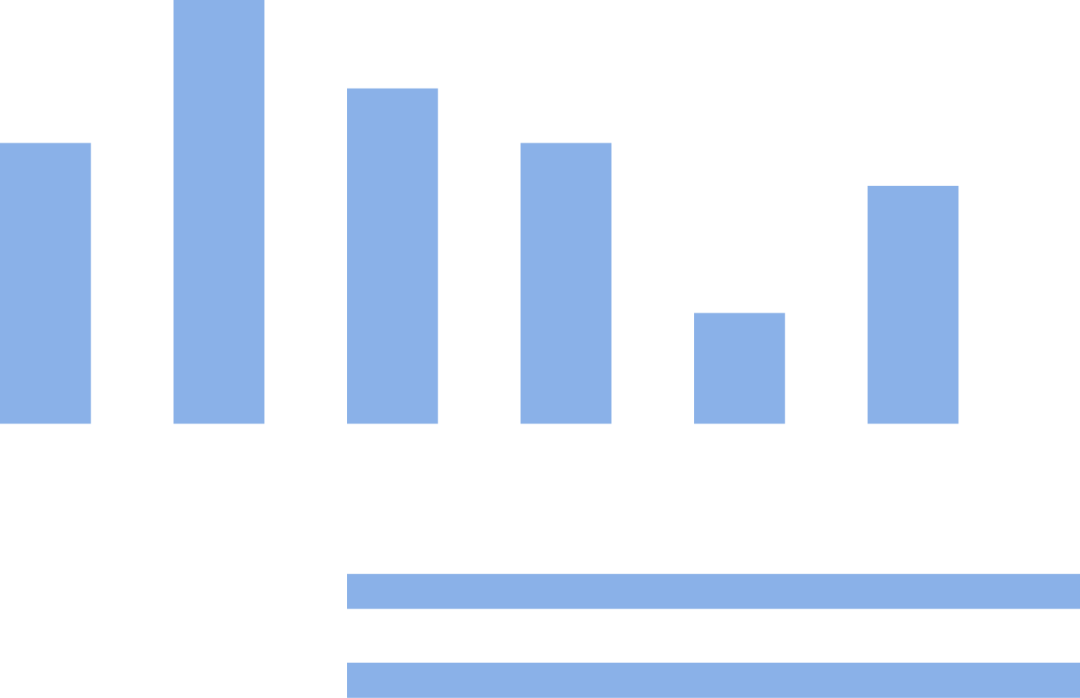
风电机组所采用的螺栓属于高强度等级,主要包括塔筒地脚螺栓、塔筒法兰螺栓、主轴螺栓和叶片螺栓,材质通常为碳钢,形状为内六角,规格范围为M20 ~ M60,长度为150 ~ 500mm。
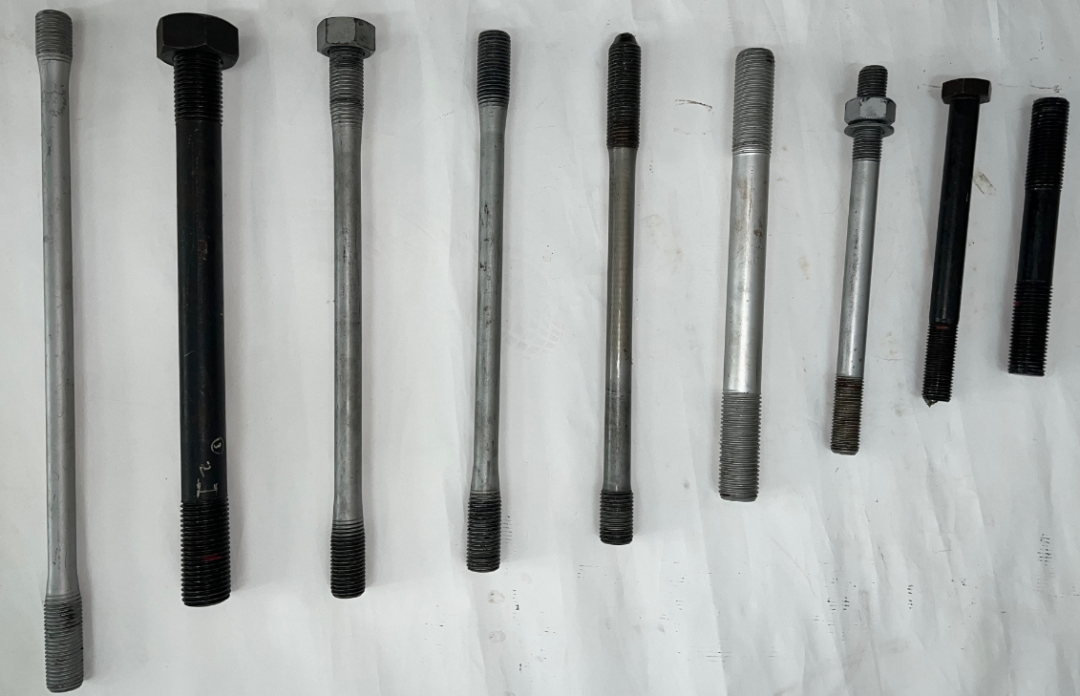
螺栓工作中除受到轴向预紧拉伸载荷的作用外,还会受到附加的拉伸交变载荷、横向剪切交变载荷或由此复合而成的弯曲载荷的作用,有时还受到冲击载荷,容易产生裂纹类缺陷,甚至发展为断裂破坏,造成叶片脱落和风塔倒塌等严重事故。
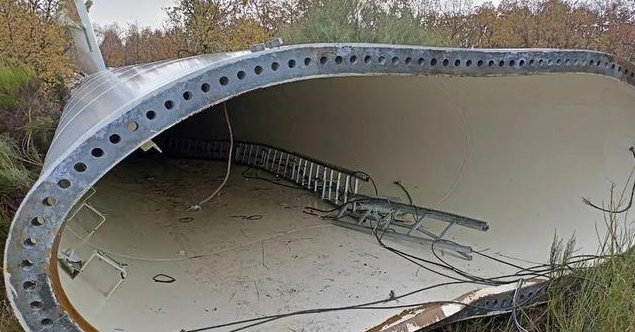
检测方法
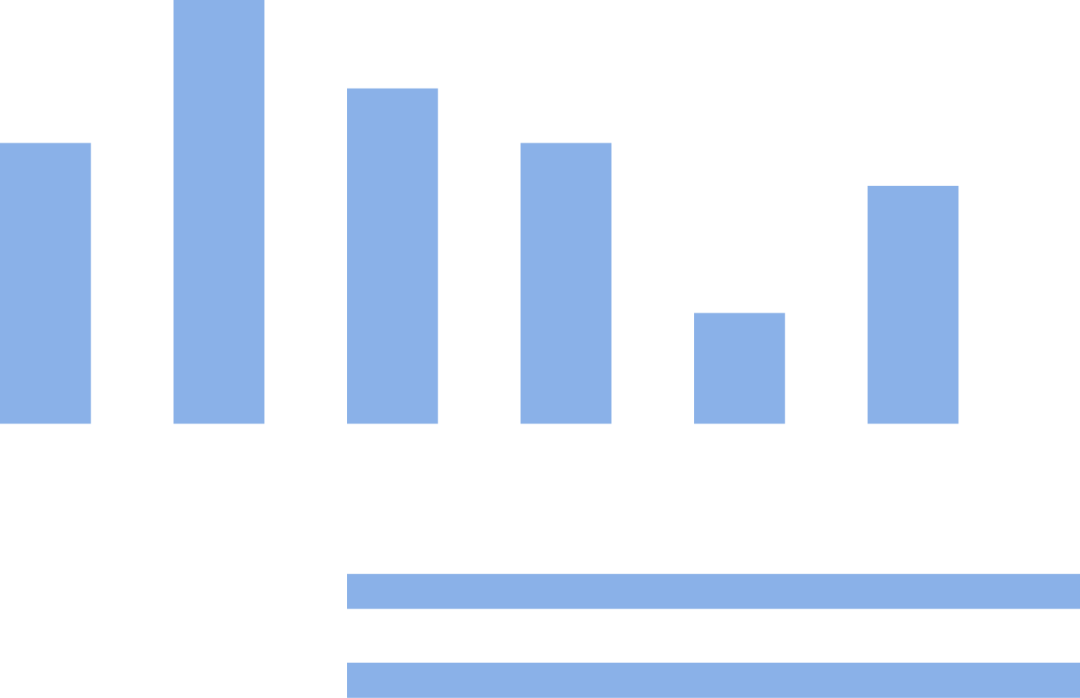
由于待检工件端面存在内六角孔,使用常规相控阵线阵探头检测信号会受到阻挡,且存在检测盲区。对此,采用菊花阵列探头进行检测是比较理想的方案,只需将探头放置在螺栓端面,通过360度圆周线性电子扫查,即可完成工件两端螺纹部位及中间光杆部位实施全覆盖检测。
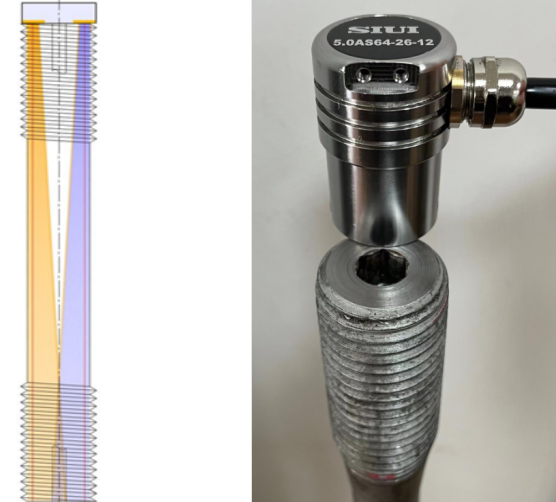
检测设备
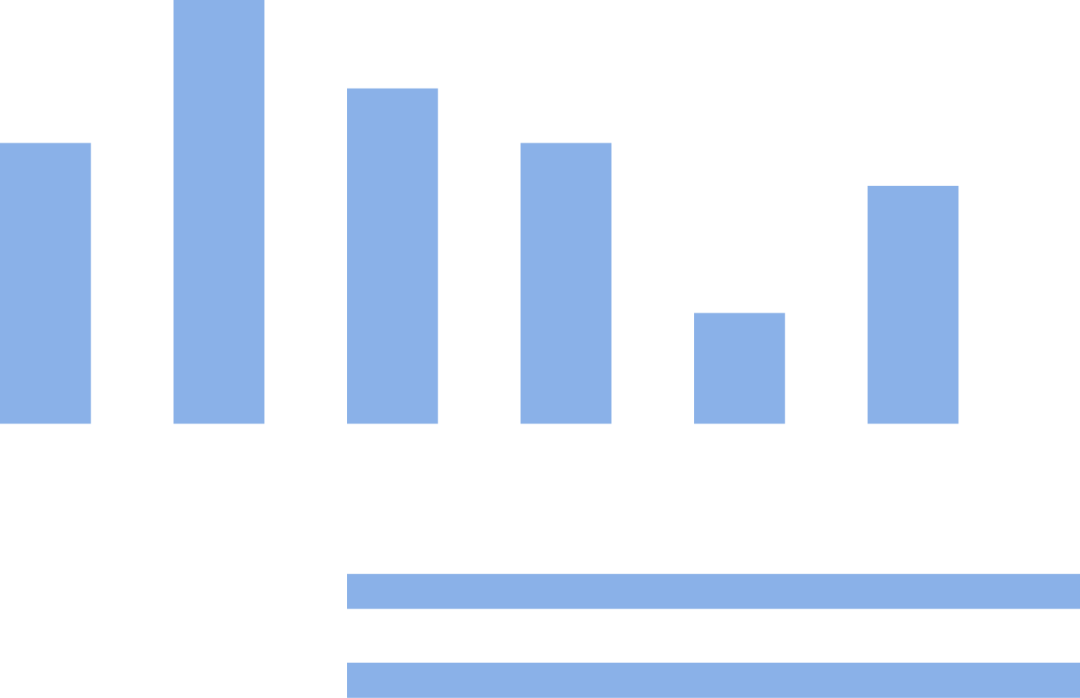
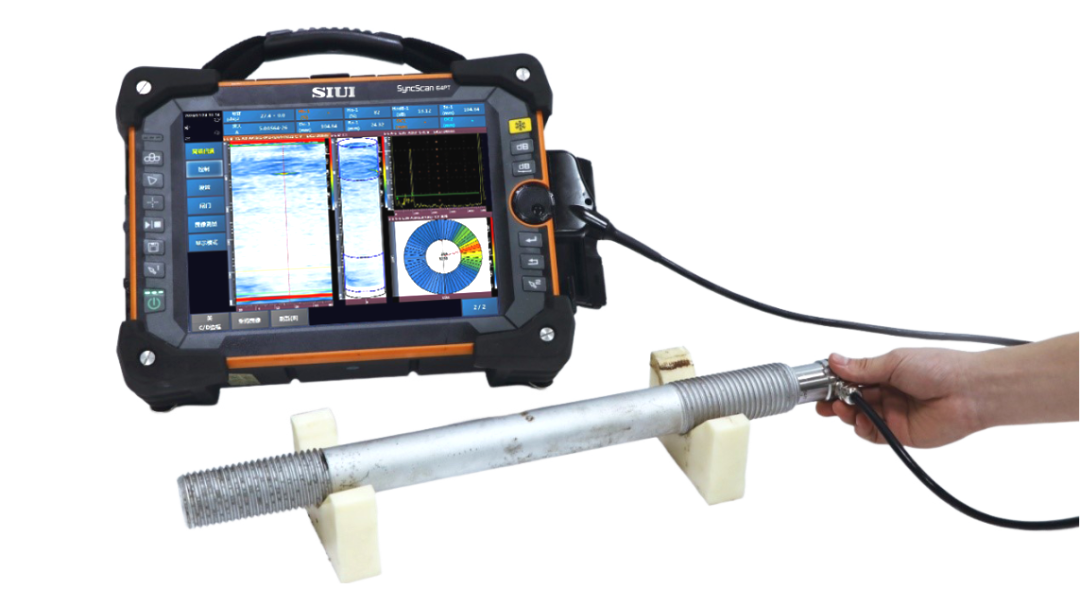


检测结果
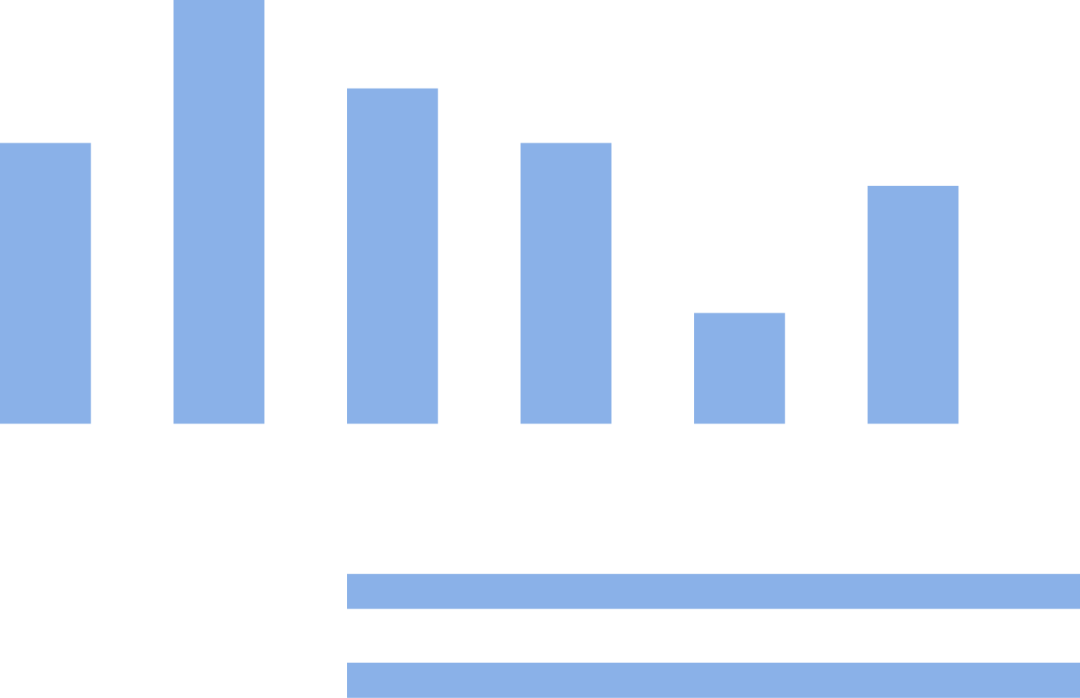
对于M34×575螺栓,可以清晰地发现2个刻槽。

经测量,深度分别为76.61mm和45.97mm,与实际工件的切槽深度吻合。
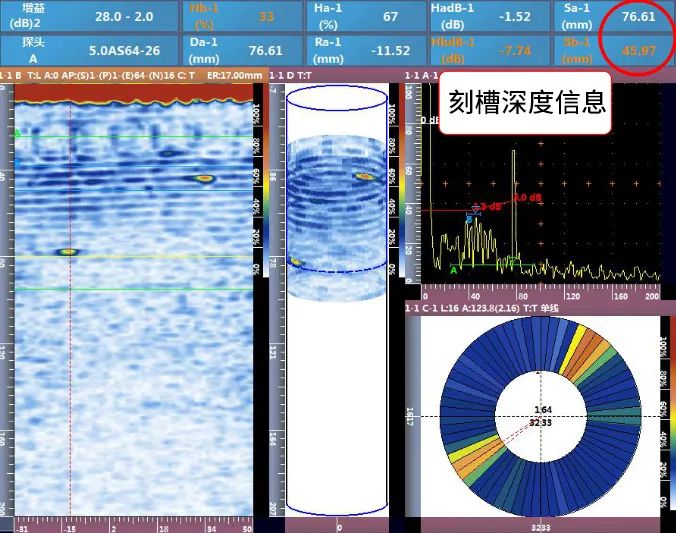
对于M38×480螺栓,可以清晰地发现1个刻槽。
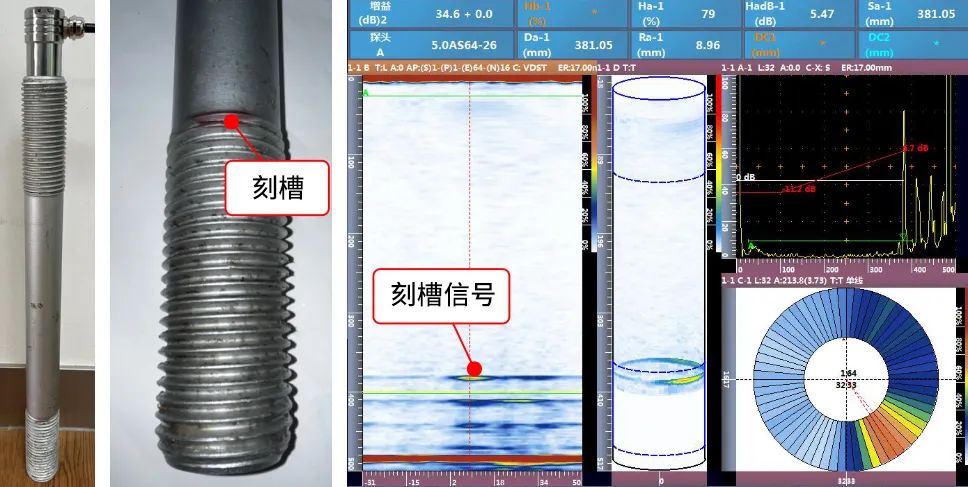
经测量,深度为381.05mm,与实际工件的切槽深度吻合。

检测现场
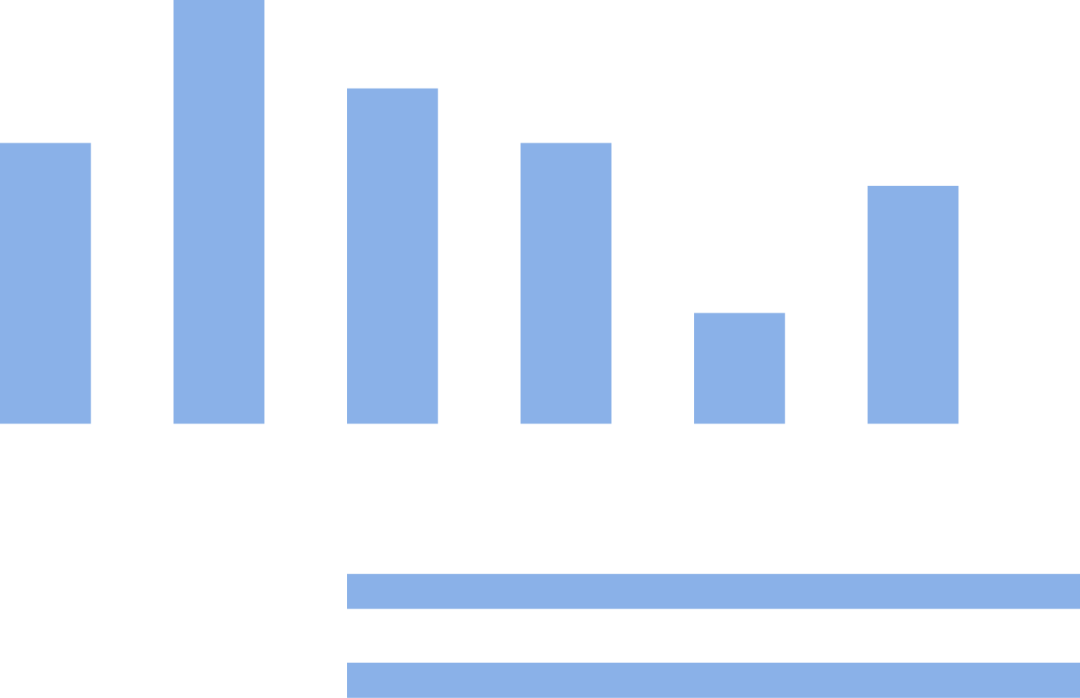
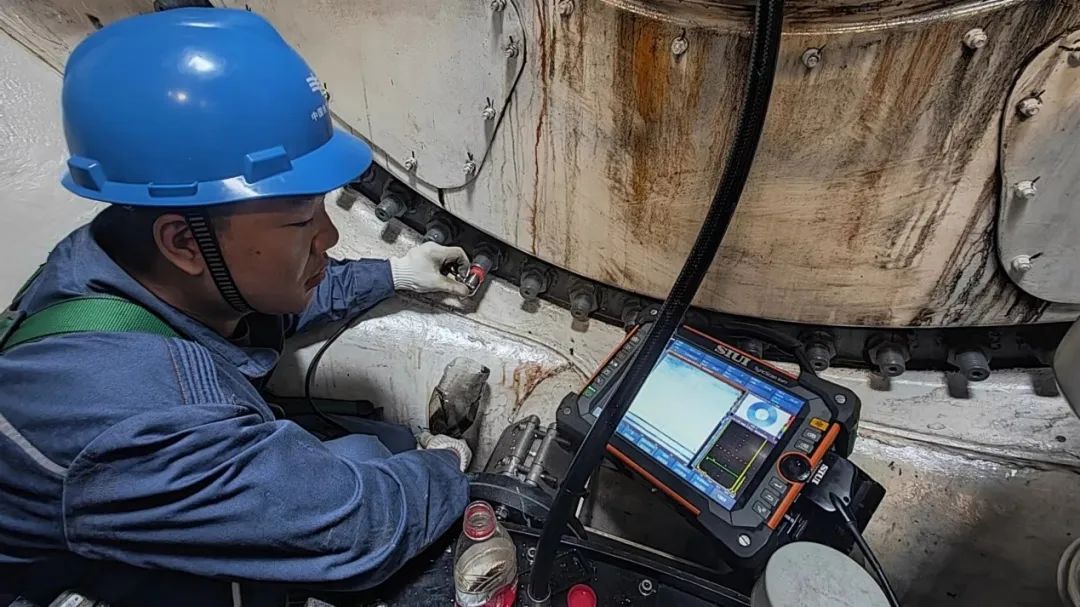
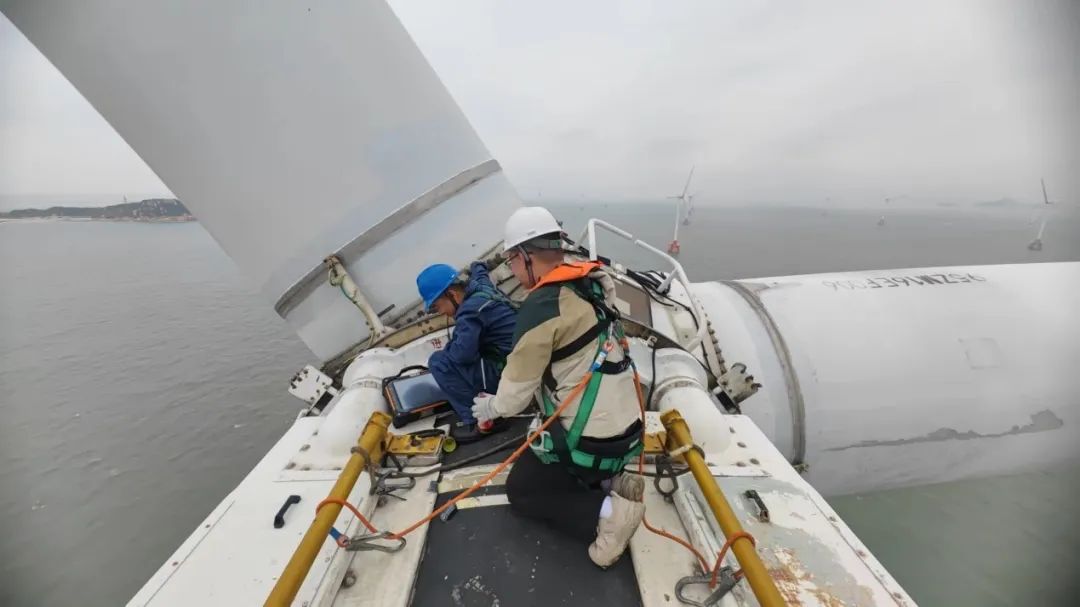
总结
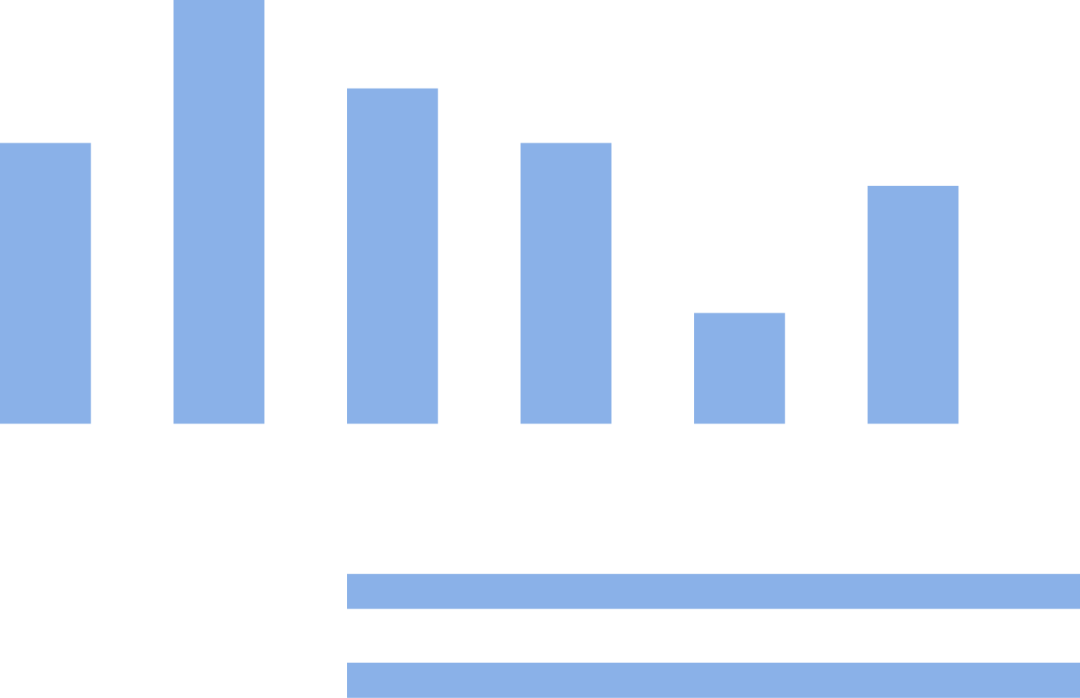
由上述实验可知,使用超声相控阵可以有效检测出风电螺栓上的裂纹缺陷,预防和避免由于螺栓破坏造成的严重事故。特别是菊花阵列探头,基于特殊的晶片形状排布,通过360度圆周线性电子扫查能够有效检测带内六角孔的螺栓,过程中不需挪动探头,是在役螺栓检测的有效、快速手段。
塔筒除了对整个机舱和叶片进行支撑,还需承受运行中随环境和工况变化产生的振动、腐蚀、疲劳和受力变化等,如果焊缝内部存在缺陷,将严重降低焊接强度,存在断裂损毁等隐患,造成重大经济损失和安全事故。为了保证塔筒的制造质量,需要进行焊接情况检测以确保其强度和安全性,塔筒制造过程的焊缝包括钢板卷圆成筒后的对接焊缝、筒节与筒节连接的焊缝、筒节与法兰连接的焊缝等,可能存在未熔合、未焊透、夹杂物、气孔、裂纹等各类缺陷。 对于上述焊缝缺陷的检测,通常采用目视检查、超声波检测、磁粉检测、渗透检测、声发射检测和射线检测等方式。目前对在役塔筒焊缝的检测,多采用绳索垂吊或建造塔架扶梯的方式进行,检测人员时刻面临着危险的高空作业环境以及长时间的体力劳动,不仅对人员健康安全构成威胁,同时严重限制工作效率和质量。
ALPHA 1006爬壁超声检测机器人系统
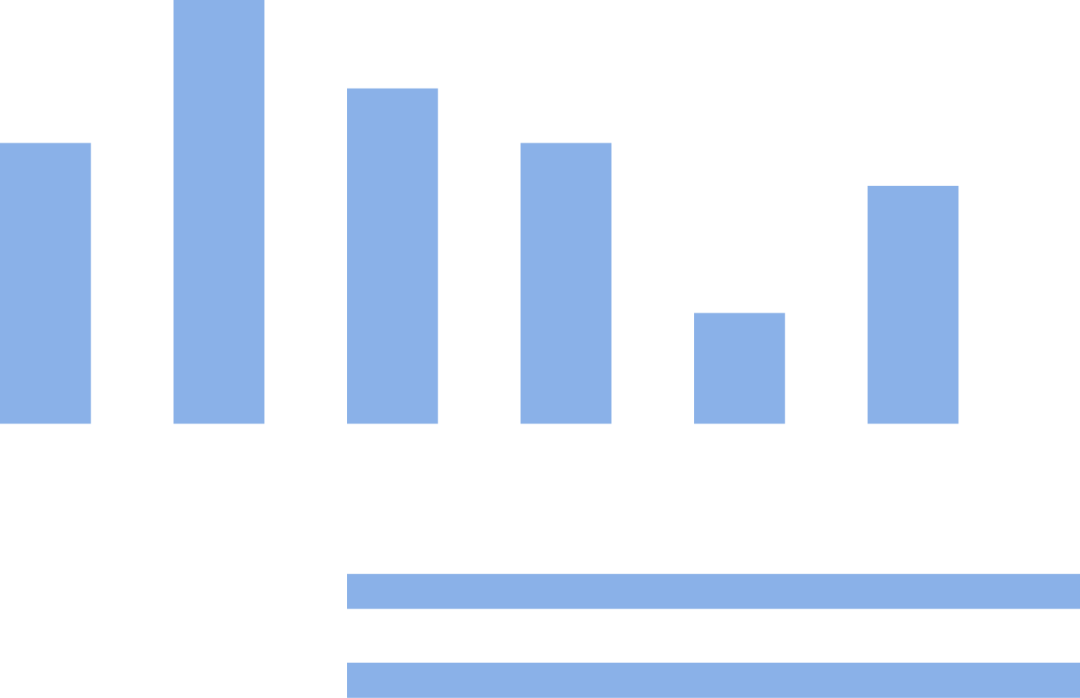
针对风电塔筒焊缝检测的种种困难和问题,汕头超声开发出ALPHA 1006爬壁超声检测机器人系统,创造性实现超声主机与爬壁机器人的集成化,检测人员得以在安全的环境下工作,大幅降低劳动难度和压力,提高工作效率。
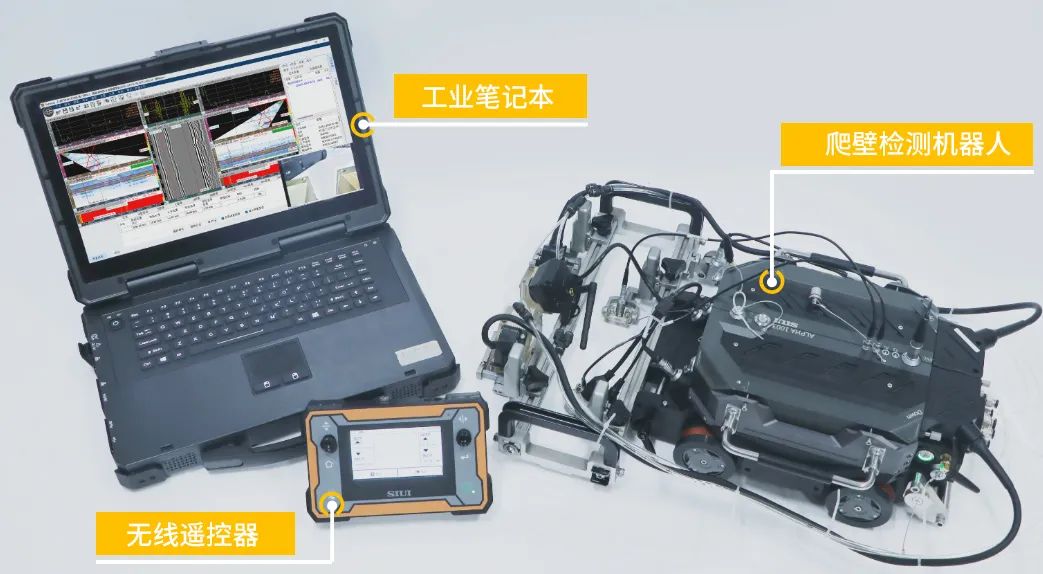
ALPHA 1006主要由爬壁检测机器人、无线遥控器和工业笔记本三大部件组成。工作过程以机器人为载体,集成超声主机和探头等设备,通过人工操控或软件智能规划,控制机器人在塔筒表面按照检测要求的轨迹移动,完成焊接质量的检测。为了适应复杂的工作环境,机器人系统完成了多项功能实现和安全考虑,得以在现场检测过程发挥出以下优势:
集成超声主机与爬壁机器人两个模块,整个系统仅1根水管与地面水泵连接
检测人员基本都在地面工作,大幅降低高空作业概率和工作风险
狭小阴暗空间的检测与常规无异,优化检测人员操作环境,降低工作难度
采用安全绳防止意外坠落
搭载多个传感器实时获取周围环境信息,对当前环境和机器人状态持续判断,提前规避可能发生问题
采用工业级磁性轮进行吸附,负载/自重比超过1
底盘配置动态调节机构,跟随塔筒表面情况自行调节磁轮高度,保证磁轮和塔筒表面紧密贴合,获得足够的吸附力
防护等级达到IP66,可承受猛烈喷水,应对恶劣复杂的工作环境
采用双电机模组驱动两侧磁轮组,在塔筒表面实现环向、纵向的移动和转弯
内置锂电池供电和无线通信控制技术,不需背负粗大笨重的供电线缆与地面的额外电源连接,运动更加轻巧灵活,运输携带便捷
避免运动过程被线缆束缚,以及线缆缠绕、破损、长距离传输信号干扰等隐患
系统配套了智能控制系统,能够根据工件尺寸和参数规划移动路径,高精度地依据路径要求在塔筒表面沿焊缝移动
距离传感器、激光导向等多个定位装置实时将机器人移动信息和情况反馈至控制系统,实现快速动态调节,保证运动精度
系统配套有无线摄像头,可实时监控机器人的运作情况,检测人员得以直观地感知周围环境和当前工作状态,根据需要随时介入机器人的操控和运动调整
工业笔记本、遥控器和摄像头的远程传输距离均达到40米,满足常规现场的检测要求
无线传输图像内嵌在操作软件,可根据需要调节显示效果等参数
系统采用模块化设计,可根据需求快速扩展适配
标配状态可实现单通道TOFD和2个相控阵探头的同时检测,最多可实现8个探头的夹持
可扩展为双轴面扫模式用于工件腐蚀检测
长输管道、压力容器等其他类型工件均可通过配置变化实现自动化检测
检测现场
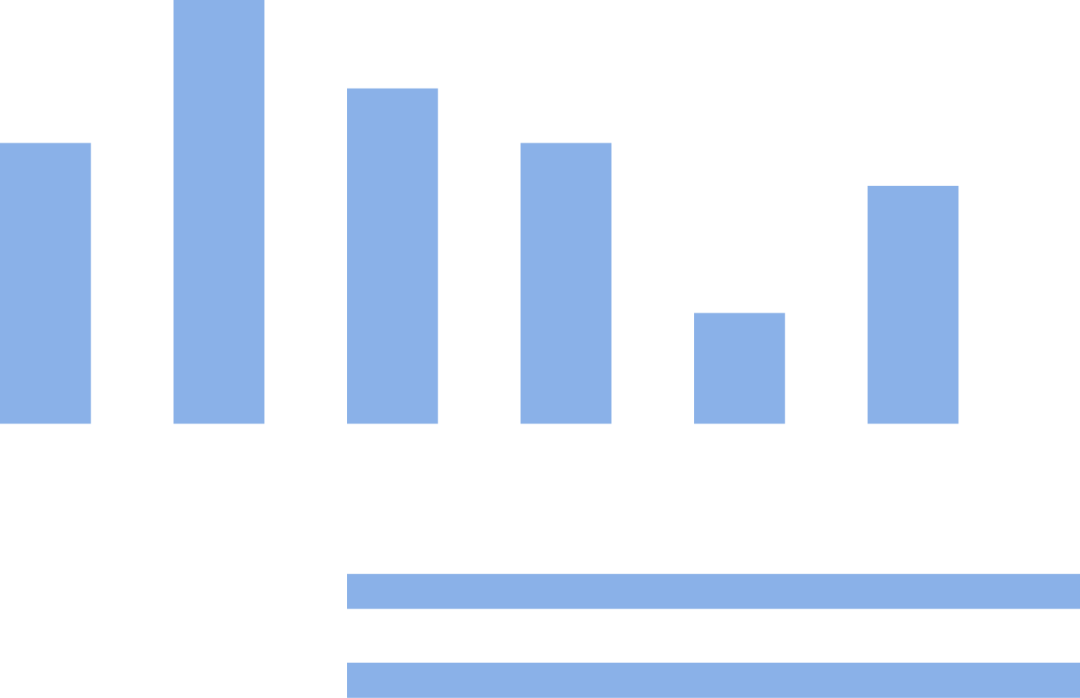
ALPHA 1006爬壁超声检测机器人系统除了应用在塔筒检测,通过变化配置可适应其他应用场景,下图是风电塔筒、球罐和大口径管等3个典型现场情况:

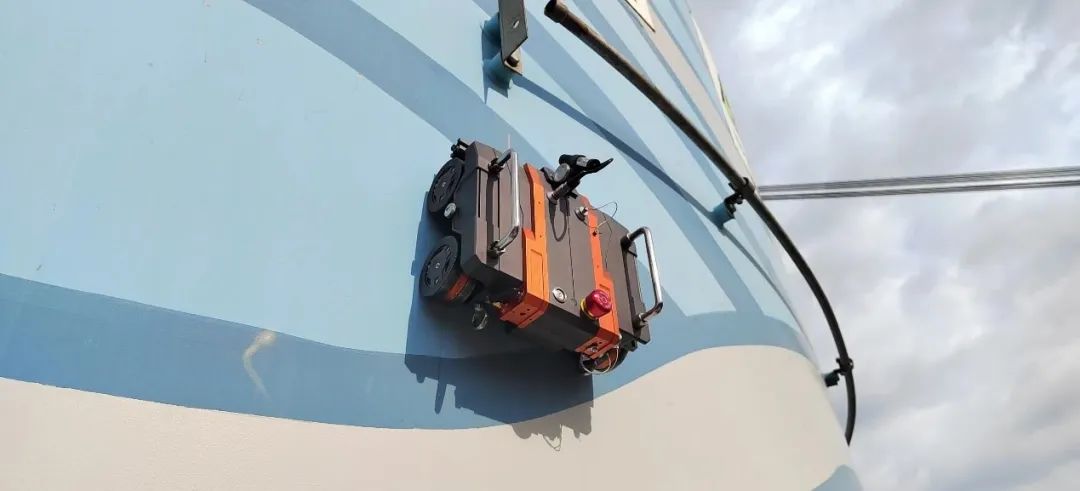