➤试箱又称吊箱试验,当集装箱船建造完工后,需对大舱箱位进行吊箱试验,以此来验证导轨间距和底锥位置是否满足吊箱精度要求。吊箱试验是集装箱船建造过程中非常重要的工艺环节。
➤传统的试箱方式需要进行试箱自检和船东报验两次现场实际试箱,工作量较大、重复作业较多、试箱的周期需要近90天!
➤如果集装箱在试箱过程中卡住或无法顺利插入底锥,则需进行大量修正和调整作业,会影响整个船坞和码头生产周期。所以造船厂急需一种新型方案,能够快速迅速地验证所造的船能否合格。
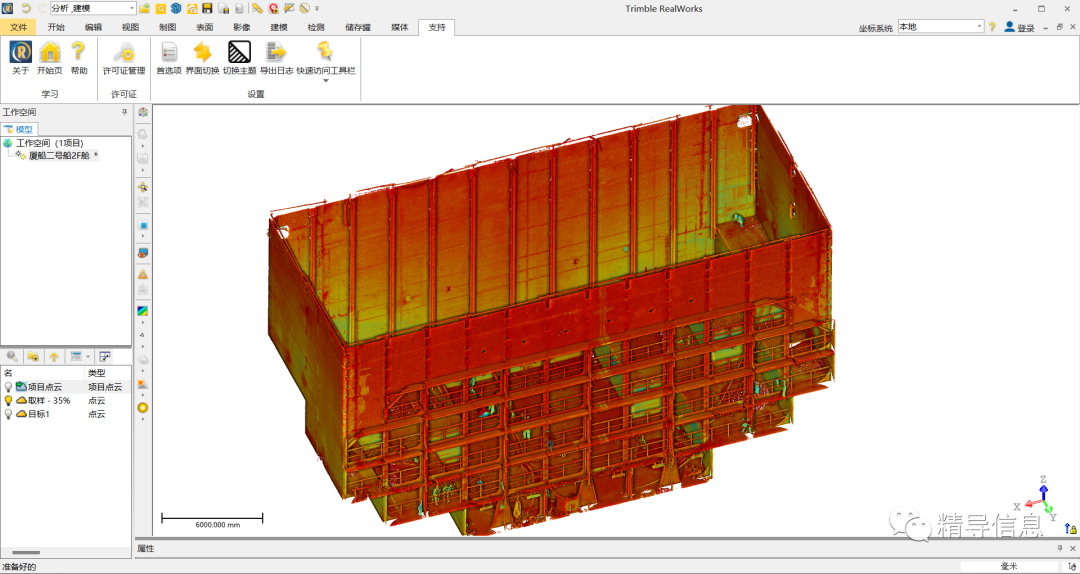
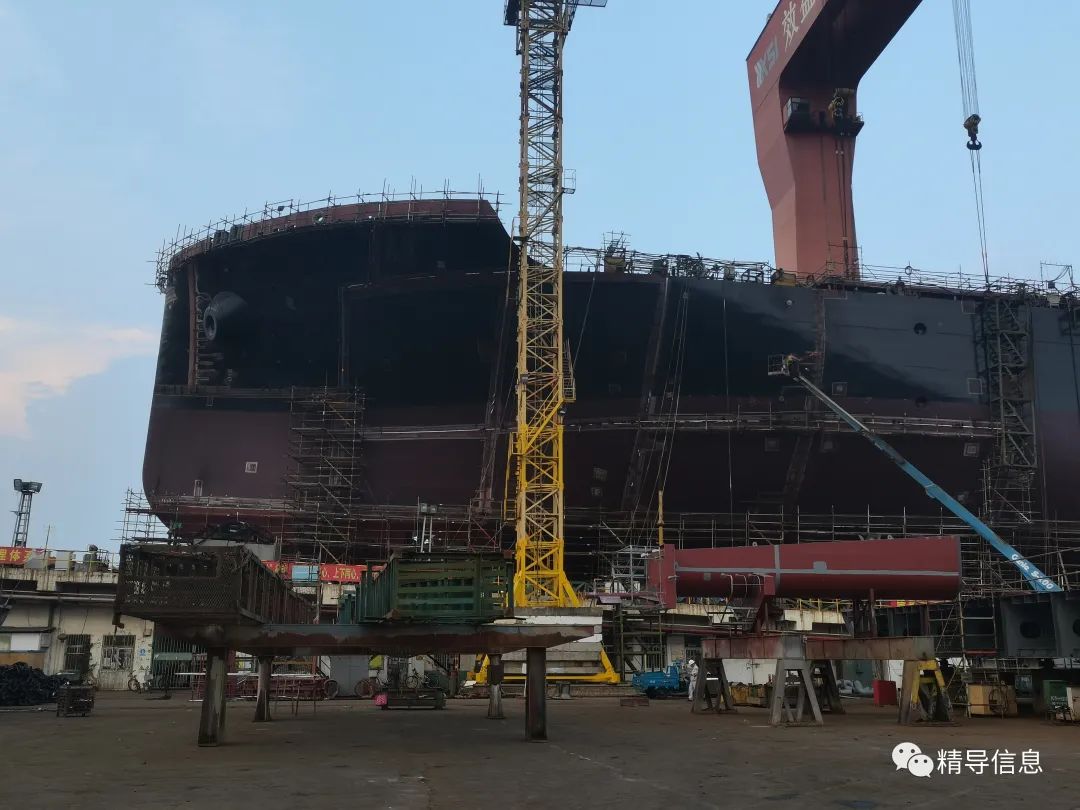
完整三维点云模型
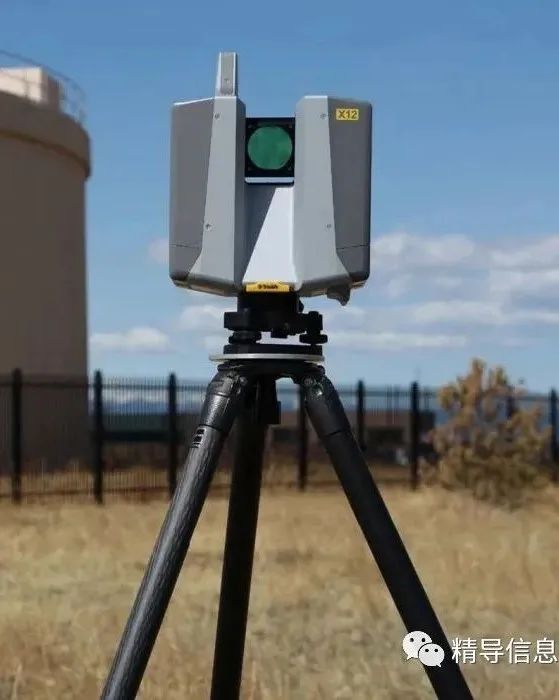
1)在船舶的密闭空间内有效作业,最小扫描范围达到业界最佳水准:0.3 米。
2)每站自动调平达3″精度,确保导轨垂直度平整度符合精度要求。
3)借助长测距、高分辨率达3mm@10m扫描(X12可达0.6mm@10m),快速采集导轨的高分辨率数据。
4)高扫描速度,导轨扫描这样精细的工作要求下,可以实现每站6分钟左右。
5)自带Trimble Perspective软件或Trimble RealWorks软件,均具整体均匀配准算法。
6)快速扫描压载舱,为后续根据 IMO 的要求改造水处理系统做好准备。
7)在船舶离开港口之前达到造船师所需的详细程度。
高精度三维点云模型
底锥等数据
➤通过数字化试箱报告进行分析,确认合格后生产部门即可对船东提交试箱报验。
➤数字化试箱的应用大大提高了箱船建造效率和试箱精确性,专业技术人员利用数据采集设备(扫描仪、全站仪等)对集装箱船货舱装箱系统(导轨、调节板、底锥、导向块)进行测量并建立数字模型,将物理空间货舱实体转化为数字空间的实物尺寸和位置关系,通过计算机软件进行去噪、拼接及分析等步骤,从而对实物精度进行更精准、有效的控制。
➤该项技术的研究和运用,使箱船试箱环节不受天气、吊车资源及人员等因素的影响,突破了实体试箱长期依赖于货舱重复作业的瓶颈,有效改善传统方法中货舱装载系统工作量大、作业效率较低的现状。