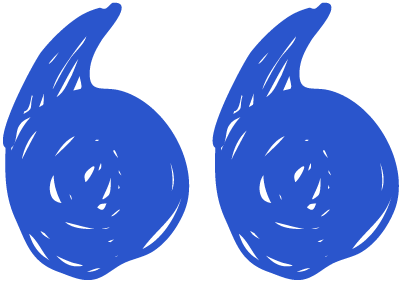
Mini 3D云台概述
本期小西为大家带来Mini 3D云台的在软包装车行业的应用分享。
使用Mini 3D云台进行中远场景(约15米)的3D数据采集,云台一次可获取多次回波数据和RSSI(能量返回值),为软包装车提供多层次的空间3D数据源,物体表面反光特性。
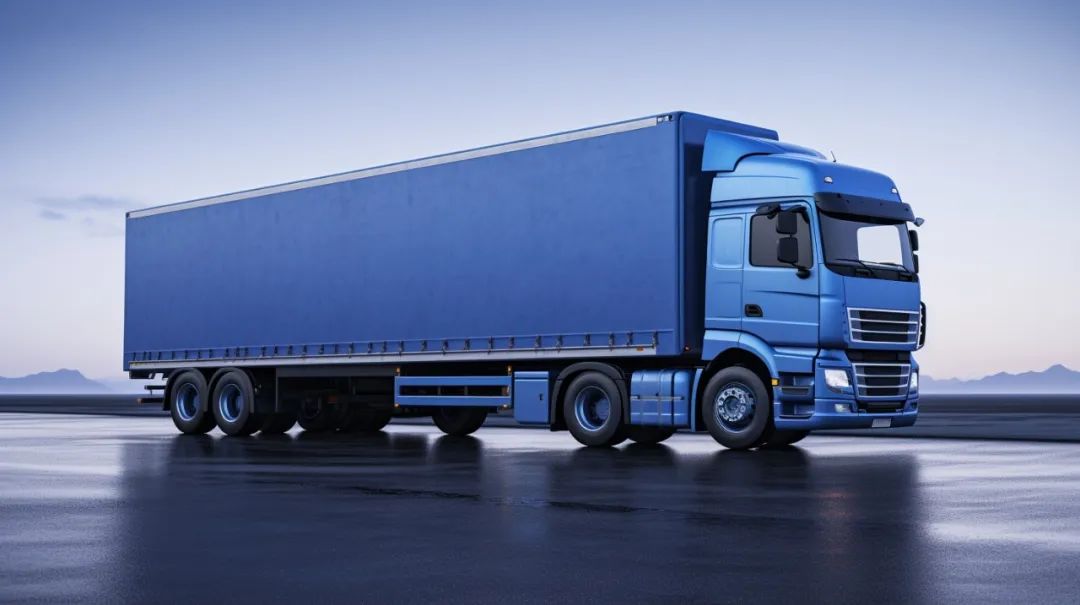
建模原理 应用 HDDM+ 实现具有多重回波功能的传感器,构成Mini 3D云台。在软包装车行业中,传感器由于光束的多次反射收到多个回波,实现多层次的物体检测,例如穿过其测量的防护玻璃、细小拉筋、雨、雪、雾或灰尘。
Mini 3D云台,运用球坐标系模型进行场景的三维复原,实现空间的精准三维建模。 HDDM+测量法 (多重回波) Mini 3D云台 建模原理
应用优势 Mini 3D云台为软包装车检测提供全面、稳定的车辆3D数据源,如具备良好的抗灰尘能力、能检测15mm细小拉筋、高分辨率及识别物体表面暗纹理等。
🔷 抗灰尘检测 Mini 3D云台具备良好的灰尘穿透力。在多重回波作用下,云台在一次扫描中,实现 “前景的灰尘” 和 “后景的被测物” 同时检测,并进行独立输出,实现精准的 “后景车辆轮廓” 的快速扫描与精准建模,如下图所示: 前景的灰尘数据
后景的车辆 轮廓数据
🔷 细小拉筋检测 Mini 3D云台专注于解决装车行业痛点:“细小拉筋” 的感知与“背景场景” 的抗干扰检测,常常是一组互不相容的命题。前者注重检测细小物体而忽略背景,而后者注重背景抗干扰检测而过滤细小物体。在实际应用,两者均同样重要,却互不相容,因此常得此失彼。
Mini 3D云台运用了HDDM+测量法(多重回波),在一次扫描中,可实现 “前景的细小拉筋” 和 “后景的车辆轮廓” 的并行扫描,且进行独立数据输出。
为软包装车中的 “前景拉筋检测” 与 “后景车辆识别” 提供准确且独立的数据源,解决两者间的互不兼容问题,为后续车辆检测提供 “拉筋” 与 “背景场景” 并行检测,如下图所示。 前景的拉筋 (专注细小物体) 后景的车辆轮廓 (专注片状区域)
🔷 高分辨率 Mini 3D云台在球坐标模型下,方位角与俯仰角均具备高分辨率的特性。
分辨率的调节,可通过设置云台扫描速度、雷达角度分辨率与雷达扫描频率来实现。车辆进行高分辨率的3D数据,为车厢后续的特征分析提供精细化与全面的三维数据源。 Mini 3D云台分辨率调节范围: ►方位角的分辨率设置:由Picoscan雷达角度分辨率决定,可选择范围有0.05,0.1,0.125,0.25,0.33,0.5。
►俯仰角的分辨率设置:俯仰角的分辨率的计算公式为,分辨率(度)=云台转速度(度/秒)÷雷达扫描频率(Hz)。
如,俯仰角分辨率0.003度(云台扫描速度0.1度/秒,雷达频率为30Hz); 俯仰角分辨率0.03度(云台扫描速度1度/秒,雷达频率为30Hz); 俯仰角分辨率0.3度(云台扫描速度10度/秒,雷达频率为30Hz)。 精细化的车辆特征
应用案例 Mini 3D云台面对着各种车型,均可提供准确有效的车辆数据源,如高栏板半挂车、平板车,凸台车等。
🔷软包袋装车的高栏板半挂车 车厢长12.5米的高栏板半挂车及其点云
🔷软包袋装车的平板半挂车 车厢长17.5米的平板半挂车及其点云 🔷托盘料装车的低栏板货车 车厢长7米的低栏板货车及其点云 🔷钢卷专用的鞍座半挂车 车厢长9.6米的钢卷专用鞍座挂车及其点云 SICK装车系统软件 (基于Mini 3D云台) 自动装车测量定位系统是一款测量顶开式车厢的测量系统。 自动装车测量定位系统是在SICK云台基础下开发的一款装车测量定位系统。其采用的模型数据来源云台扫描所采集的数据。
通过分析与计算数据,获取空车车厢的底板,栏板,拉筋等结构部位的全局位置与尺寸信息,将结果以客户全局坐标系的形式发送给客户,从而让为客户进行精准的自动化装车作业提供稳定的、快速且可靠的车厢信息。 SICK自动装车测量定位系统的主界面 SICK装车系统装车应用案例一 (车厢12.5米的高栏板凸台车) SICK装车系统装车应用案例二 (17.5米的平板型凸台车)
🔷SICK装车系统(基于Mini 3D云台)的适用车型