作为一种前沿的尺寸测量和数字建模方案,高精度3D视觉技术正深度应用于古老的铸造工艺领域。从模具制造到铸件整修,从成品质量把关到新品迭代优化,高精度3D视觉技术与各个环节的创新融合,展示出加速铸造行业实现质量与效率跃升的强大动力。
铸造是一项多工序集成的制造工艺,要求从模具制造至产品成型的每一环节都要进行精准的尺寸检测。这样全流程的尺寸质量控制,是铸件品质的坚实保障。
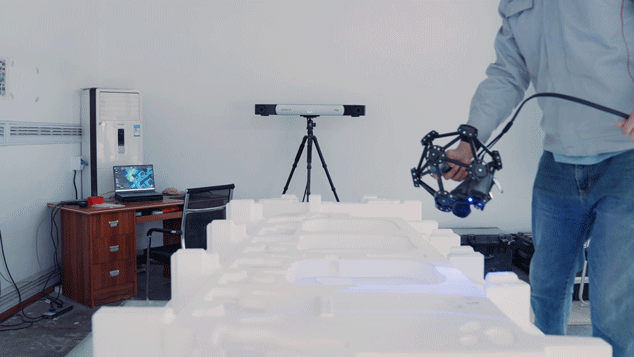
传统的模具检测手段主要依赖人工测量和接触式检测技术,这些方法不仅效率低,而且对模具的不规则曲面及内部复杂结构覆盖不足。相比之下,高精度工业3D扫描仪以非接触、无损、全面的尺寸测量能力显著提升了模具验收的精度与效率。
以FreeScan Trak Pro2这类大范围跟踪式激光三维扫描系统为例,在对大型铸件的消失模进行检测时,该系统实现不粘贴标志点的激光三维扫描,高效流畅地获取消失模完整三维数据,大幅缩减了三维尺寸检测所需的时间,为后续铸件浇筑生产流程节约了时间资源。
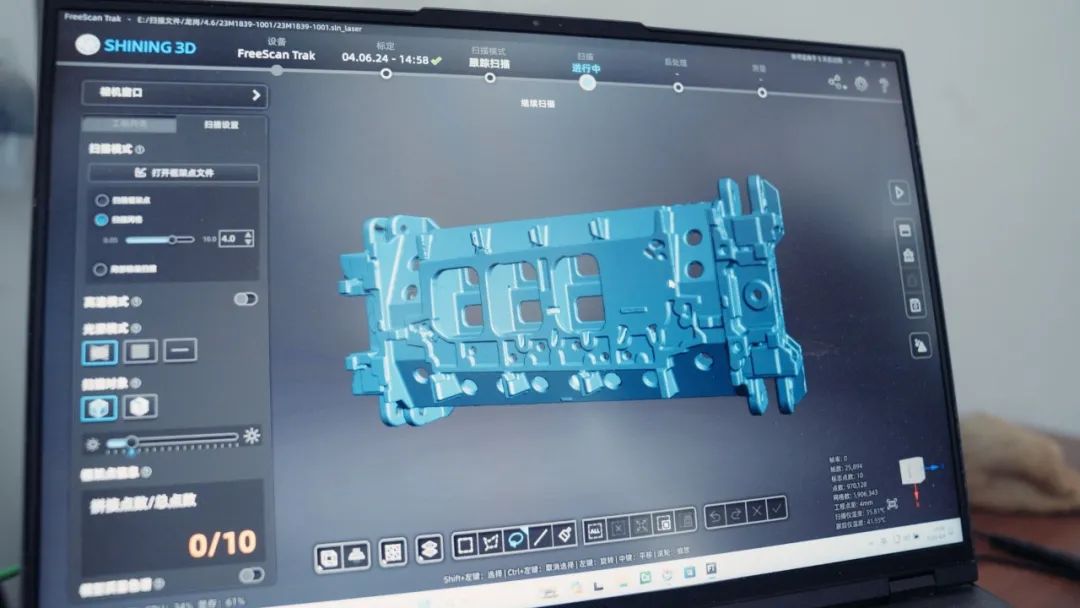
这类经过深加工的铸件,其尺寸精度直接影响到与其他组件的装配吻合度以及整个系统的运作效能。因此,精准控制加工余量,防止因加工过度或加工不足引发的尺寸偏差,对确保此类铸件的品质至关重要。
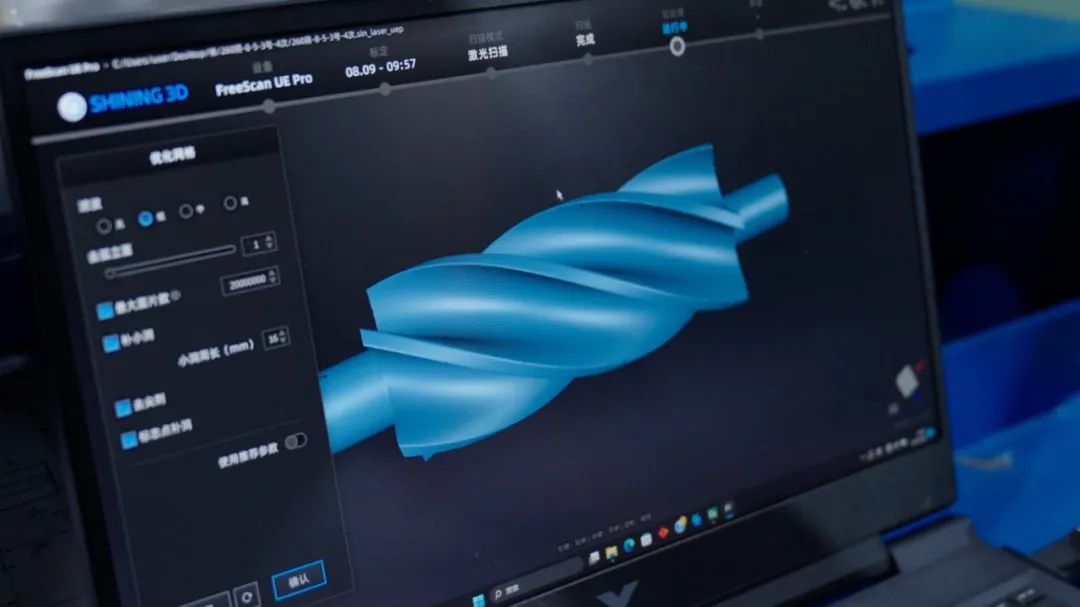
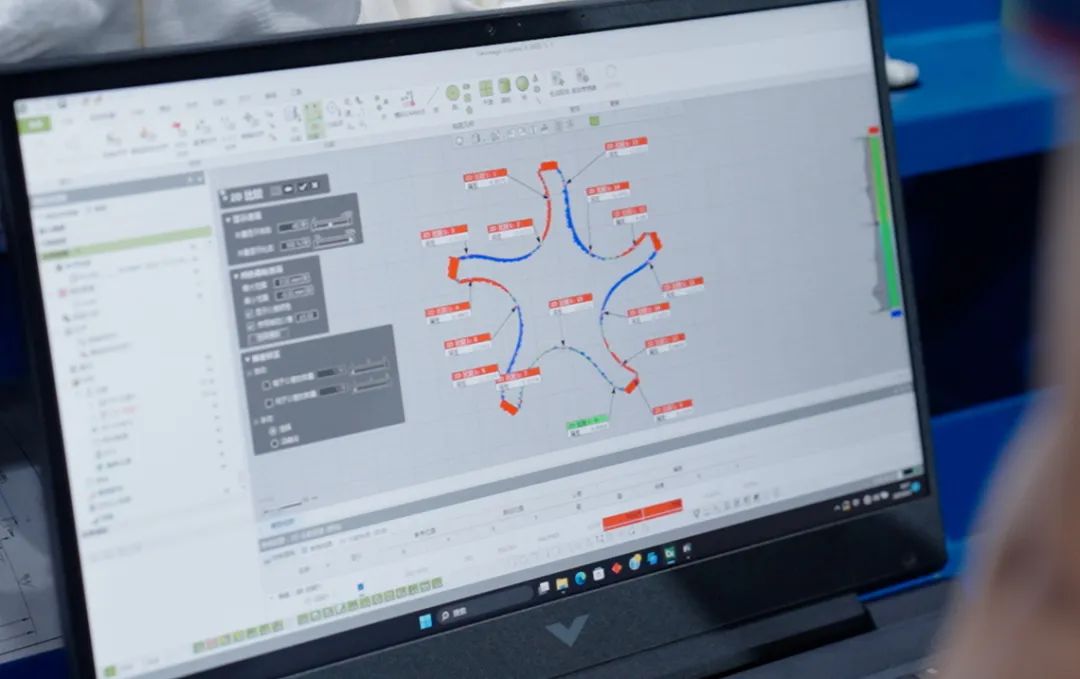
成品质量检测是铸造质量控制的收尾环节。将高精度工业3D扫描仪获取的三维数据导入检测软件,与原始设计图纸对比,即可量化所有不符合规范的部分,生成直观、翔实的检测报告。这种可视化的检测结果,不仅保证出厂铸件达到严格的质量标准,还为用户提供了可追溯的审核依据。

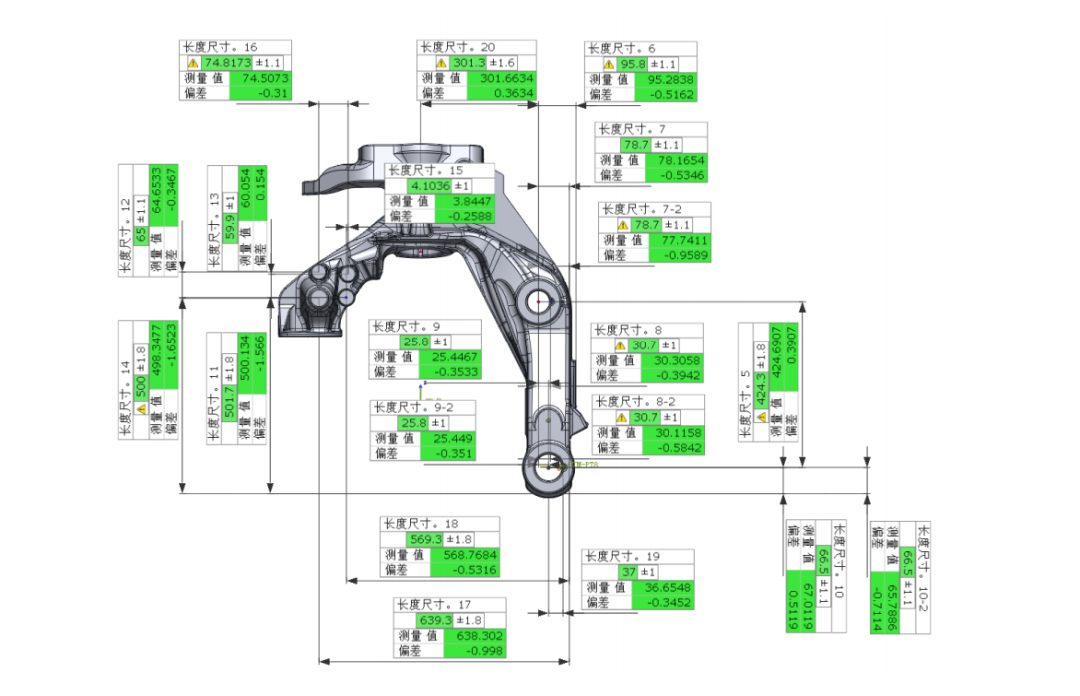
值得一提的是,针对铸件内腔检测的特殊需求,可对铸件进行切割,使其内腔暴露,再分别捕获各个部分的三维数据。完成扫描后,借助先临三维配套软件强大的数据处理能力,实现内腔断面数据的无缝拼接与融合,构建出完整的内腔三维模型,保证铸件内腔结构的全方位尺寸检测。

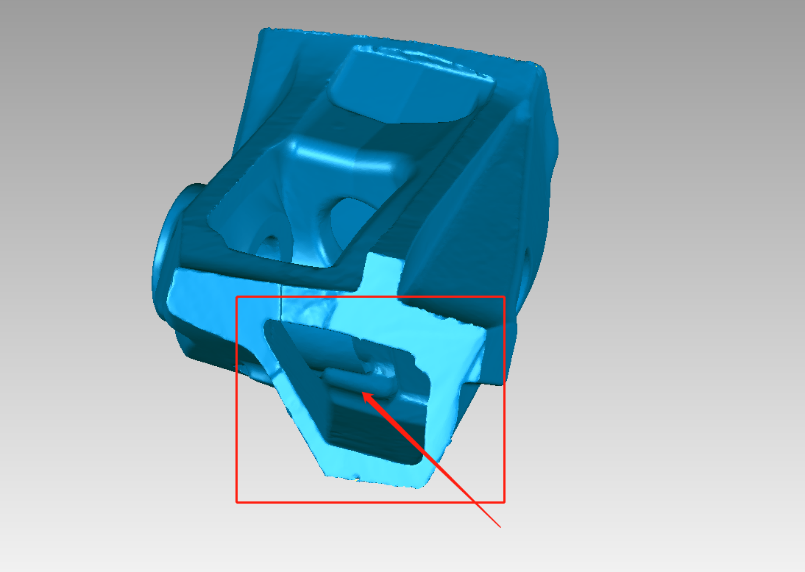
铸件的三维数据不仅是尺寸质量控制的依据,也是产品优化的重要反馈。
一方面,先临三维的高精度工业3D扫描仪可以快速获取铸件三维数据,为大量尺寸检测数据的统计与分析提供支持,进而揭示铸件设计上的潜在问题,如结构不合理致使加工困难、公差分配不当导致装配困难等。

另一方面,利用三维扫描获取的数据,可对现有铸件进行高精度建模。以增压器涡壳的新品优化设计为例,设计师可以基于这一3D数模进行局部修改、结构调整或者性能优化。这种基于实物数据的迭代设计,相较于从无到有的设计方式,大幅提高了设计的针对性和成功率。
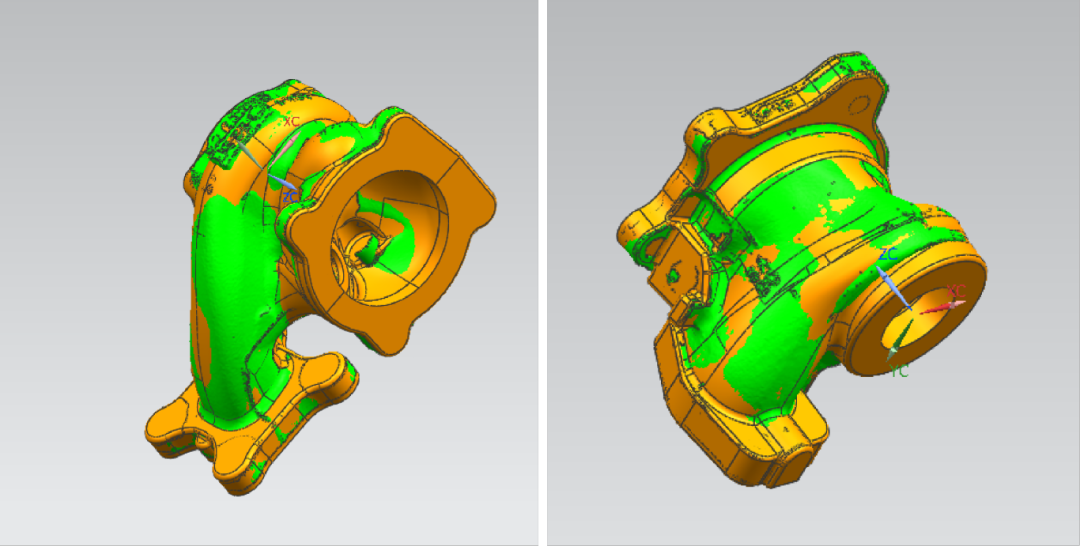