“数字中国”战略正日益成为产业转型升级的强大引擎。以数字化转型为核心,驱动能源行业向低碳、绿色、高质量发展,既是当务之急,也是大势所趋。
将3D数字化技术引入能源行业装备制造各个环节,能够助力构建清洁、低碳、安全、高效的现代能源体系。
案例中的客户为某大型汽轮机厂,是我国从事电站动力设备和新能源开发与制造的国有重点骨干企业。公司产品种类涵盖火电、核电、气电及新能源等多个领域,现已成为国内乃至世界先进的发电机设备制造中心,全国三大汽轮机制造基地之一。
重型汽轮机是发电和驱动领域的核心设备,被誉为装备制造业的明珠,是一个国家科技水平和综合国力的象征,也是我国突破发达国家技术封锁的关键设备,该项目的圆满完成对国家重型高端装备制造业具有重大的战略意义。
在这个案例中,我们将向您展示3D扫描仪如何助力大型汽轮机铸件全尺寸三维数据采集、加工余量分析及精准划线,为能源企业装备制造控制成本、提质增效。
案例中的工件为汽轮机排汽缸,排汽缸作为连接汽轮机末级叶片和凝汽器的重要部件,直接影响着汽轮机组的热效率。因此,严格控制排汽缸铸造精度,完善铸造工艺流程,可以极大提升汽轮机生产制造效率,提高企业核心竞争力。
客户需要对直径6m的排汽缸进行全尺寸测量,以获取铸件模型,结合加工模型进行对比分析,确定各个角度余量是否充足,并根据余量情况制定加工程序。
在没有余量的情况下,需要确认基准借量是否充足,如果借量不足,则需要进一步确认缺料位置及所需增材的量。
同时,还需要借助虚拟划线进行辅助划线,确认加工基准切割位置及20个窗口位置。
客户之前的检测的方式,都是通过人工在铸铁平台上划线,检查余量是否充足,并寻找基准位置。传统划线的测量方式存在诸多缺陷:
1. 测量效率低下,每调整一次测量位置,就必须重新寻找基准线,耗时耗力。
2. 难以找到最佳基准线位置,十分依赖工人的经验。
3. 无法进行虚拟划线,导致无法精准辅助划线位置,会造成一部分合格品被判断成非合格品或次品,造成加工成本的增加。
使用设备:跟踪式三维扫描系统、测量光笔

1. 扫描(1小时)
借助跟踪式三维扫描系统快速扫描铸件模具,得到铸件整体数据模型。
2. 对比分析(10分钟)
将三维扫描数据和数模进行对比分析,查看是否都存在余量;确保有余量的情况下,寻找最佳基准状态,保证后续加工过程中每个加工面都有加工余量,以减少后期加工成本;在余量不足时,找到需要增材的部位,并给出增材量。
3. 光笔划线(时间约为2小时)
使用测量光笔,根据分析的情况进行基准划线,在需要加工位置的窗口划线。
4. 划线,得到准确的加工基准及窗口位置。
跟踪式三维扫描系统采用智能光学跟踪测量技术,无需贴点,操作简易,在扫描和划线时,设备能随时移动,极大提升了工作效率,1小时以内即可完成全尺寸三维数据采集。
三维扫描仪为一体式球形设计,主体框架为碳纤维材质,坚固耐用、轻巧便携,设备不易受震动、温度等现场条件的影响,具有超强的性能稳定性。
标记点在球体框架上均匀分布,无论三维扫描仪切换至何种角度和位置,都能被跟踪仪精准捕捉,轻松高效完成扫描任务。
1. 扫描获取三维数据,借助软件与原数模进行对比分析,形成直观的色谱偏差图。
2. 利用专业的软件,根据加工工艺调整加工基准,保证每个加工面都有加工余量,从源头减少废品率。
方案中使用跟踪式测量光笔,结合光学跟踪器,快速辅助进行基准划线,并在需要加工位置的窗口进行划线。
此外,再通过软件进行虚拟划线,提前判断划线位置是否准确,从而指导后续划线和加工过程,更大程度保证划线效率,缩短制造周期。
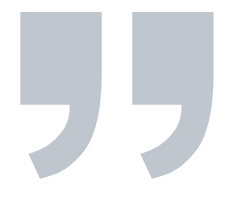
客户评价
针对大型铸造件,中测科技可以快速给出精准高效的三维测量方案,帮助我们快速分析产品余量,指导制定加工程序,进行辅助划线。
借助3D扫描设备,使整个工艺流程更加标准化,大大降低了对人工经验的依赖程度,提高了生产成功率,减少废料,为我们节约了生产制造成本。同时,也缩短了铸件生产周期,是降本增效的理想选择!
中测科技致力于提供高效专业的数字化测量方案,优化装备加工工艺流程,助力高端装备制造业打造安全可控、自主可靠的装备产业链,以数据驱动企业降本增效,为绿色能源保驾护航。