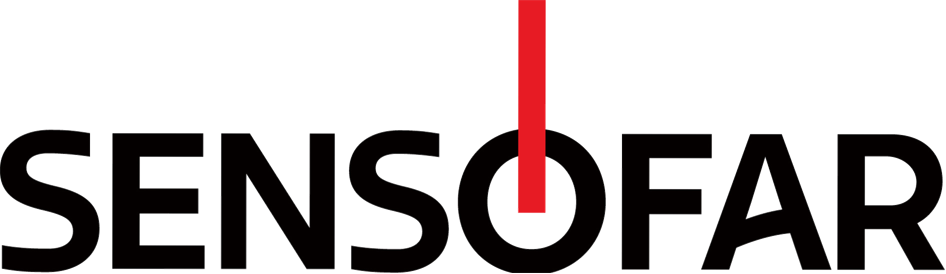
增材制造工艺中的形状与表面纹理变化
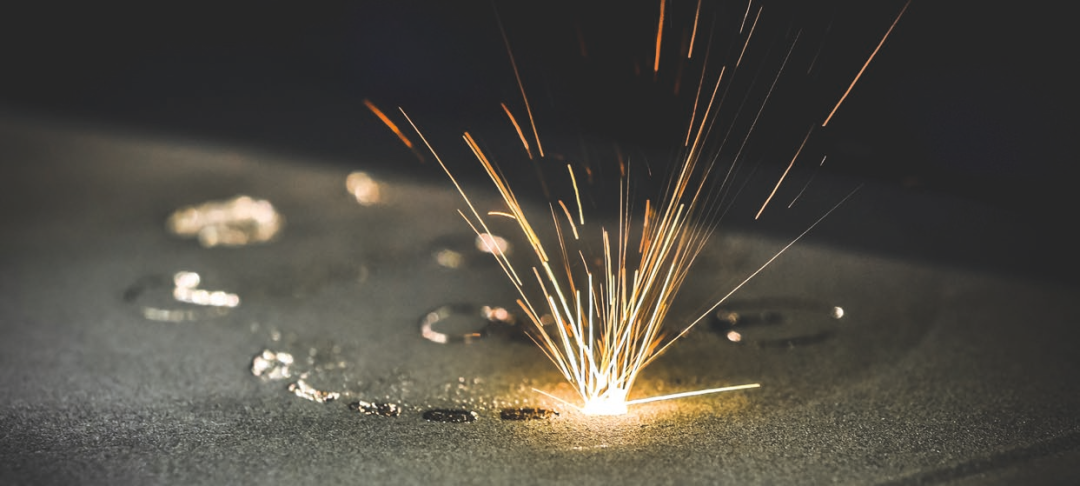
与传统的减法和成型方法相比,增材制造具有诸多优势,因此在过去十年中被行业内广泛采用。
增材制造在制造复杂几何形状方面所提供的可能性是传统制造方法无法比拟的。然而,它也有
一些缺点,如缺乏标准化、难以控制生产样品的尺寸和表面特性,以及在大多数情况下需要后
处理步骤。在这项研究中,我们希望通过测量形状和表面纹理来衡量单一参数对制件最终
属性的影响。

测量
在本案例研究中,我们使用了选择性激光熔融技术,用两种不同的材料制作了两次相同的试样。
通过这种方法,我们希望了解这种变化对制造部件整体形状的影响。我们选择钛合金 Ti6Al4V
和铝合金 AlSi10Mg 作为测试材料,因为这两种材料在航空航天和医疗行业中应用广泛。
我们用 S wide 3D轮廓测量仪测量了这两个样品和一个参考样品,并用 3D 对比软件进行了比较。
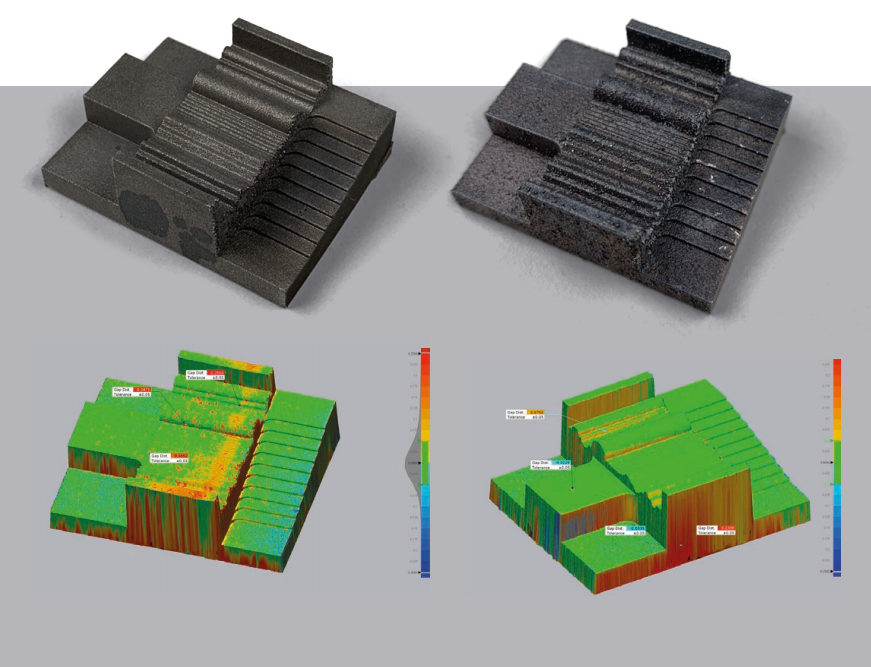
图 1. 制造的样品照片及其三维对比的截图(左:Ti6Al4V;右:AlSi10Mg)。
3D 对比显示了 SLM 制造样品与参考样品之间的差异。我们可以看到,偏差较大的部位是在样
品几何形状的边缘,但两种材料都能保持整体形状。不过,铝合金样品表面的某些位置偏差较
大,这是由于球化效应造成的。
我们还进行了类似的测试,但当时使用的是用相同材料制造的两个样品,并改变了 SLM 机器的
一个内部参数(光束补偿)。这一次,由于预期偏差较小,我们使用了 CAD 文件作为三维对比
的参考,而不是参考样品。
事实上,这才是控制生产的最合适方法:在 CAD 模型的不同区域设置一些公差,然后根据这些
公差分析生产出的零件。
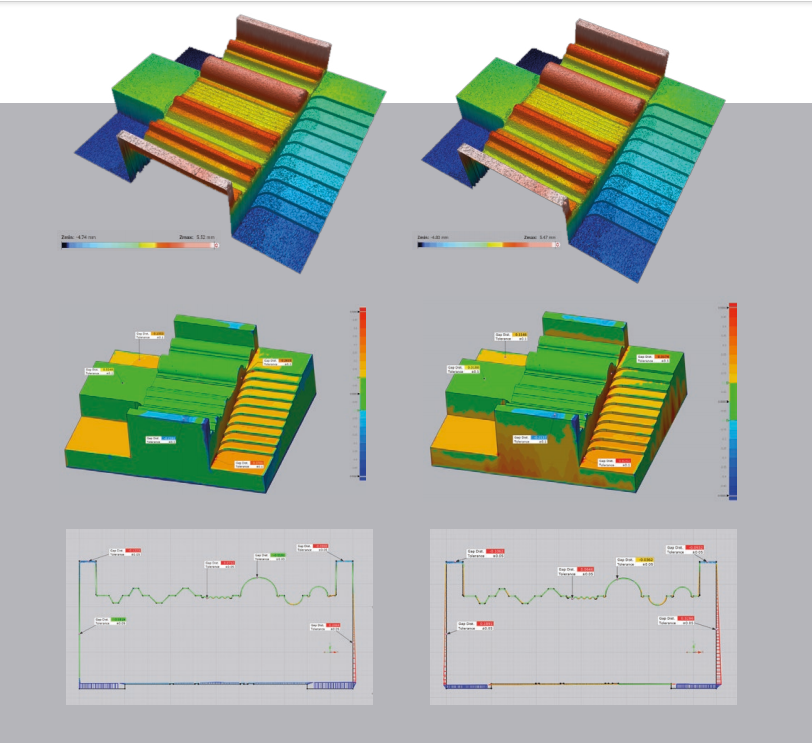
在图 2 中,可以看到一个样品和另一个样品之间的差异,突出显示了一些关键点。我们还可以
选择一个横截面,分析每个样品的轮廓是如何变化的。下一步将回到制造过程,调整参数,使
输出始终符合我们的预期。
制件的表面纹理对其功能性能至关重要。因此,了解增材制造过程中的不同变量如何影响不同
的表面纹理参数是一个热门研究课题。
在第二个案例研究中,我们制造了另一个测试样品的不同单元(1 cm x 1 cm正方形,厚 2 mm)
,但改变了角度。这是对使用增材制造的制造商和研究人员的共同考验,其目的是了解其机器
这些情况下的性能。
我们使用 S neox 3D 光学轮廓仪测量了不同样品多个位置的表面纹理,并将样品垂直于光轴
定位。然后根据 ISO 25178 标准,使用相同的嵌套指数对测量结果进行过滤,以确保进行有
意义的对比,最后使用 SensoPRO 软件进行比较,以确定哪些参数可区分每组测量结果。
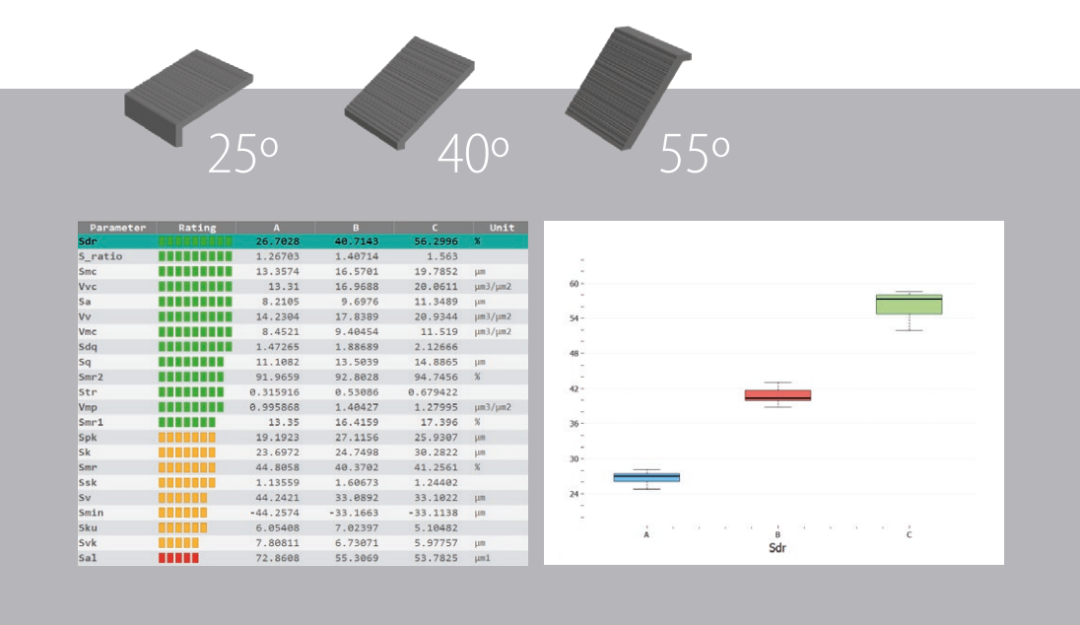
结果表明,角度的变化,表面纹理也会随之变化,具体来说,我们得出的结论是,变化最大的
参数之一是 Sdr(显影面积比)。Sdr 参数在与增材和涂层相关的应用中十分常见,因此对于功
能性能与附着力来说的涂层相关的增材制造表面(如疏水表面)来说,角度至关重要。
结论
在第一项研究中,我们分析了增材制造过程中的一个单一参数如何改变所生产样品的形状。在
第二项研究中,我们还通过识别特征表面纹理参数,定量区分了不同角度的样品。
采用边缘投影技术的 S wide 3D轮廓测量仪用于形状测量,而 S neox 3D 光学轮廓仪则用于表
面粗糙度测量。在 S neox 3D 光学轮廓仪中,AI多焦面叠加技术因其速度和 HDR 模式而成为测
量微米级粗糙度的理想选择。然而,共聚焦技术和干涉测量技术(也包含在同一系统中)正被
用于表征各种增材制造部件,从初始表面到光滑的后加工表面。由于在同一系统中集成了不同
的光学测量技术,S neox 3D 光学轮廓仪的多功能性已被证明是十分有用的。