应用案例 Case study 微流体应用中激光加工微通道的测量
由于应用领域众多,微流体在过去几年中取得了巨大的发展。芯片实验室、芯片器官、点护理设备、细胞捕获、生化分析是微流体直接应用的一些例子。微流体设备具有不同的几何形状,可以根据需要任意调整,但组成这些微流体设备的基本结构之一是微通道。
有几种材料已经被公开可用于制造微通道,材料的适用性取决于制造技术。其中一些材料是聚合物、硅或玻璃。制造技术的例子包括软光刻技术、光刻技术或热熔技术。但在使用钠钙玻璃作为材料时,由于其坚固性、耐腐蚀性、透明度和低成本的直接激光写入技术成为最合适的技术之一。它既精确又通用,能快速生成非常复杂的几何形状。此外,由于其非接触性质,不会产生污染物,也不需要无尘室设施。
在该应用中,当尺寸达到微米级时,则需要有关通道尺寸的形貌图像支撑,以确保其质量,通过共聚焦显微镜对激光直接写入技术制造的结构可进行全面的测量鉴定。
测量
微通道是通过直接激光写入在钠钙玻璃上制作的。该装置由一个振镜系统组成,该系统能够处理光束并制造复杂的结构,且无需移动样品。通过使用焦距为100mm的透镜将激光束聚焦在基材表面上,确保工作面积为80x80mm²。
为了获得结构适当的纵横比,对样品进行了多次激光写入。因此,我们对表面的演变进行了研究。制造了扫描次数从一到十次的微通道。运用我们S neox 3D光学轮廓仪,使用20倍放大倍率的物镜捕获结构化区域的共聚焦图像。生成表面轮廓,并描绘了微通道深度随激光扫描次数的变化情况(图1)。
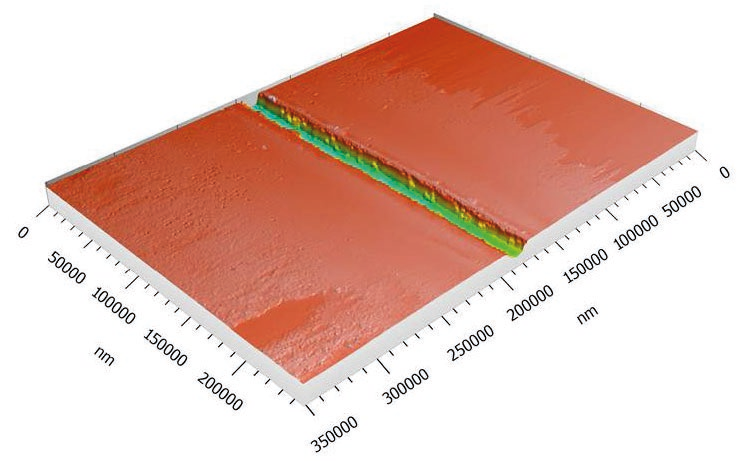
图2. 根据 ISO 25178 标准,激光加工微通道的三维图和通道底部的粗糙度参数。
微通道壁的粗糙度值是关键值,因为对于微流体应用来说,该值必须足够低。通过我们S neox 3D光学轮廓仪和SensoMAP 分析软件的帮助下,能够从小区域获得粗糙度值。研究选择了用50倍放大物镜来测量进行8次激光写入的微通道底部图像(图2)。

由于激光直写技术的多功能性和精确性,我们可以制造出多种微流体设备。在此,我们展示了其中一些用共聚焦 20X 物镜获得的3D图(图 3)。
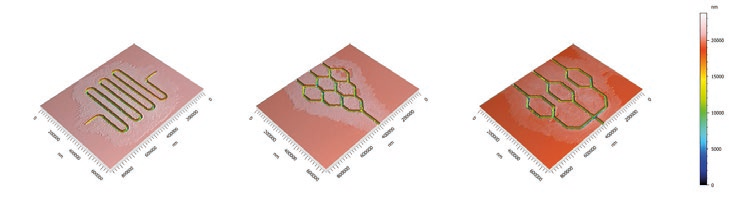
结论
通过使用我们的S neox 3D光学轮廓仪,能够轻松测量使用激光技术制造的微通道的形貌。使用20倍放大物镜的共聚焦技术,分析激光写入过程中结构轮廓的变化。
此外,结合SensoMAP分析软件,计算了制造的微通道的粗糙度参数。在获取表面形貌时,采用了50倍的放大物镜。
总之,通过使用S neox 3D光学轮廓仪,可以完美且精准地对每个结构的尺寸和粗糙度进行表征测量。